Water carves steel, stone at GlacierJet
Candace Chase | Hagadone News Network | UPDATED 14 years, 10 months AGO
At GlacierJet Technologies, owner Joshua Boyce harnesses the power of water and crushed garnets to precision-cut thick slabs metal or stone into works of art or industrial parts with no hazardous waste, toxic fumes or dust.
From a small shop on Ash Road in Evergreen, Boyce serves clients from artists to the aerospace industry using the versatility of his OMAX water jet cutter.
Because water cutting creates little heat, the process allows very fine and intricate cuts on every imaginable material.
“It’s really limitless — there’s no limit on intricacy or pattern,” he said. “I can cut everything from foam, rubber or wood to six-inch steel.”
On Thursday morning, Boyce stood back with his client Jerry Murphy, watching his $200,000 machine deftly carve a bison historical marker for one of the stops on the new Lower Valley Driving Tour.
Murphy, president of History Is Posh, was amazed.
Boyce had the same reaction when, as an apprentice machinist at his father’s Precision Engineering business, he saw the finely machined parts created by an out-of-state subcontractor using a water jet cutter.
“It fascinated me that they could cut steel with water,” he said.
According to industry lore, a forestry engineer first experimented with water to cut wood in the 1950s. The concept didn’t take off until Mohamed Hashish added abrasives to the jet several decades later, powering up the potential of water cutting.
In 2003, Boyce translated his fascination into GlacierJet Technologies. He researched the equipment and found the two main manufacturers, OMAX and Flow, in Seattle.
Deciding that OMAX best suited the parameters of his business, Boyce purchased the equipment consisting of a Dell computer that guides the water jet cutter around the 5-by-10-foot cutting table immersed in a 7-by-13-foot water-bath tub.
Boyce took two weeks of training before opening his doors in December 2003.
“My machinist background was really helpful,” he said.
Boyce also had computer experience with computer-assisted design systems that cut down on his learning curve. He perfected his operating skills in the slow months while he grew his new business.
“It went pretty quickly,” he said. “Our peak year was 2007. I was running two shifts, 18 hours a day.”
GlacierJet found a good demand from artists in the Flathead Valley and beyond. Inexpensive shipping options, a quick turn-around, quality product and lower business costs made his services attractive to out-of-state electronic and aerospace industries as well.
“Hewlett-Packard is one of our customers,” he said.
A wall in his office displays samples of his artistic, intricate cutting capability, including a finely cut musical bar for a chandelier and a multi-piece circular marble inlay for a high-end home.
“We do a lot of industrial parts like replacement parts for lumber mills,” he said. “We also do a lot of signs, a lot of letters and knife blanks.”
Boyce once built a lifting mechanism for NBA scoreboards that allow a camera to drop 30 feet for close up shots, then zip quickly back up. GlacierJet also has produced a number of gun parts such as triggers that require super-close tolerances.
He said he really enjoys artistic projects such as History Is Posh’s historic site markers inspired by artist Nancy Dunlop Cawdrey’s bison painting, “One is the Sun.”
The production of the markers began with Boyce scanning the bison picture into the computer portion of the equipment and tracing the outline to create a cutting file. He then adjusted the dimensions and inserted the name of the historic site such as Demersville or Ashley.
“Once I have the drawing set, it gives me a preview,” Boyce said. “I look at the geometry of the cut and decide which side of the line to cut on.”
He placed a 4-by 8-foott piece of 3/16 inch thick mild steel on the cutting board in the water bath. This water bath diminishes the cutting force of the jet after it passes through the steel.
“If there was no water reservoir, the machine would actually cut a hole through the floor,” Boyce said.
When he powers up the equipment, a pump pressurizes water to 55,000 pounds per square inch that passes through a water inlet narrowed down by a diamond with a .014-inch hole. After passing through the diamond, water mixes with the crushed garnet in a tube to form a jet that cuts the steel, starting with a powerful surge as it makes the first pierce.
To avoid clogging the tiny diamond passage with mineralization, the water goes through a purification process including softening and passing through four filters.
“Evergreen has really hard water, Boyce said.
Because cool cutting allows close nesting of cutouts, he figures he can get nine bison out of the sheet. He said the high yield from materials is another benefit of water jet cutting.
Depending on the number of letters on the bison, the cutting process takes between 20 and 30 minutes.
“It’s three times faster than machining, so it’s real competitive with plasma and laser cutting,” he said.
Once he has the bison cut out, Boyce sandblasts the markers to remove the oxide scale coating from the steel mill so the piece accepts an acid bath to create a decorative rust finish before applying a clear coat.
“That gives it character,” Boyce said.
Murphy plans to install the first 150-pound bison marker at the Demersville site at 8 a.m. Monday morning. Delivery of the pieces marks the completion of another custom project by GlacierJet Technologies.
Although the recession has cut back the volume of projects, Boyce still finds a lot of satisfaction with the work.
“The thing I like best, what’s really satisfying, is you have something you created at the end of the day — something that you can hold in your hands,” he said.
For more information, consult the company’s website, glacierjet.com.
Reporter Candace Chase may be reached at 758-4436 or by e-mail at cchase@dailyinterlake.com.
MORE IMPORTED STORIES
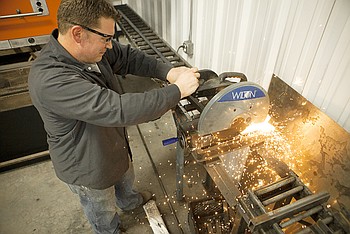
On the cutting edge: Acutech expands waterjet, ironwork capabilities at new facility
Daily Inter-Lake | Updated 13 years ago
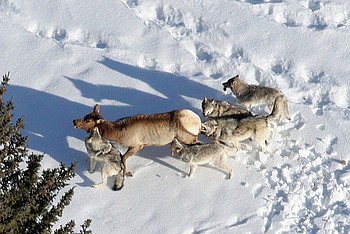
Reflecting on the 40 years since wolves reintroduced in Yellowstone
Bonner County Daily Bee | Updated 6 years, 4 months ago
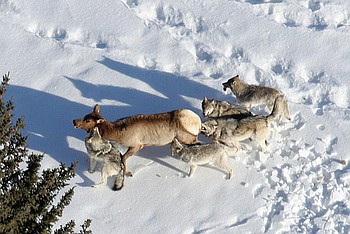
Reflecting on 40 years since wolves were reintroduced in Yellowstone
Coeur d'Alene Press | Updated 6 years, 4 months ago
ARTICLES BY CANDACE CHASE
Dogs' tale touches people's hearts
Amber, the silver Labrador retriever rescued from the cold with nine puppies, became an overnight celebrity since her story and photos of the family appeared in Saturday’s Inter Lake.
Red Cross blood supply critically low
MONTANA — The American Red Cross has issued an urgent call for blood donors since the supply has reached critically low levels for blood types O positive, O negative, B negative and A negative.
Dogs' tale touches people's hearts
Amber, the silver Labrador retriever rescued from the cold with nine puppies, became an overnight celebrity since her story and photos of the family appeared in Saturday’s Inter Lake.