Students craft prosthetic hands
HILARY MATHESON | Hagadone News Network | UPDATED 10 years, 5 months AGO
Specialized three-dimensional printers can make almost anything one can imagine — food, clothes, instruments, car parts and human tissue. Even basic 3-D printers can make more than just plastic trinkets.
Seventeen-year-old Georgia Donaldson wants to make a prosthetic hand for a child using Whitefish High School’s MakerBot 3-D printer.
The Whitefish senior and her advanced chemistry teacher Todd Spangler are looking for a specific candidate — a child who has missing or underdeveloped fingers and can control his or her wrist movement.
Creating the prosthetic hand is part of a yearlong project for Donaldson’s advanced chemistry class. Spangler’s advanced chemistry students each selected an area of interest to complete research projects. Spangler suggested Donaldson use the school’s 3-D printer to make a prosthetic hand.
Donaldson was very interested in plastics engineering. She became really interested in three-dimensional printing after attending a National Youth Leadership Forum: Engineering and Technology program at the University of California, Berkeley over the summer. Before that she had toured the engineering studies program at Western Washington University where she learned more about the technology.
“They [Western Washington] had this polymer engineering technologies unit that was making tons of things with 3-D printers,” Donaldson said.
Donaldson set to work researching various prosthetic designs online including Robohand, a South African-based nonprofit. She contacted hand therapist Ty Esham of Robohand USA to learn more about the organization.
Donaldson said Robohand was created by Richard Van As of South Africa after he lost his fingers in a woodworking accident in 2011. Unable to find a proper and affordable prosthetic to replace his fingers, he began to develop his own. Van As employed the help of Washington-based mechanical special effects artist Ivan Owen.
In 2012, they successfully designed a working prototype and in 2013 turned to 3-D printing technology to cost-effectively manufacture the prosthetic.
Donaldson downloaded free open-source digital blueprints Robohand published online at www.thingiverse.com.
In addition to designing blueprints, people can purchase hand kits and parts from Robohand USA. Spangler purchased two Robohands for demonstration purposes. Donaldson held one of the assembled hands up to show how it worked in Spangler’s classroom Wednesday.
Like its namesake, the Robohand looks like the jointed skeleton of a robot hand. The simplistic design functions with a pulley-style system to do a basic grabbing, grasping motion. Donaldson pointed to wire cord threaded through the prosthetic hand like tendons. When the wrist bends, the wires pull all the digits downward. To retain resiliency, elastic cord is also threaded through the hand, Donaldson said.
If they are able to find a child who needs a prosthetic, a hand cap and gauntlet made out of medical-grade Orthoplastic would need to be molded to the individual to attach the prosthetic hand and comfortably fit over the residual limb. Orthoplastic is used for its breathability, Donaldson said.
“We don’t want it to be pressed against the skin because that can cause abrasions,” Donaldson said. “There’s a lot that has to go into these to make sure they’re functioning but still cheap — that’s harder to do — so that’s what Robohand has been working on.”
Nearby, the MakerBot blocked out digits using a Robohand blueprint. The machine pulls a spool of polylactic acid filament into a heated nozzle or extruder. Polylactic acid filament is a plastic derived from biodegradable ingredients such as cornstarch. The melted plastic begins to “draw” the design on a platform. After one layer is completed, the platform moves down and another layer is drawn. Layer by layer, the digits begin to take their 3-D shape.
While Donaldson is using predesigned digital blueprints, Ryan Boyle, an industrial technology teacher at the high school, has his advanced CAD students create original designs that are converted to a file that is readable by the 3-D printer.
“They’ve gone from building a 3-D shape on the screen and never really being able to see it — to being able to hold it,” Boyle said.
The advantages of the 3-D printed prosthetic is price. It is a fairly inexpensive alternative — $150 for an unassembled basic hand kit, not including the hand cap or gauntlet — compared to standard prosthetics that cost thousands.
“We’re looking for a child because with them parents definitely don’t want to pay for prosthetics because they grow out of it really easily and they have to buy more,” Donaldson said.
Finding a child that meets their criteria has proven difficult. Spangler has contacted area doctors, physical trainers and Shriners Hospitals for Children in Washington.
He also contacted Doug Jack, a certified prosthetist/orthotist at Northern Care in Kalispell. Although Jack didn’t have a candidate, he said it was interesting to hear about the project.
While 3-D printing is catching on, it is not yet mainstream. Jack said he is not very familiar with 3-D printed prosthetics such as Robohand, but said it sounded like a technology that may impact the industry as it evolves and becomes more refined.
“We’ll see where it goes,” Jack said.
Donaldson said she is looking forward to seeing what the 3-D printing world has to offer in the future.
“We’re interested in looking at the advancement of this technology as well. Since this is open source, a lot of people have been doing different things with the hand,” Donaldson said.
Reporter Hilary Matheson may be reached at 758-4431 or by email at hmatheson@dailyinterlake.com.
ARTICLES BY HILARY MATHESON
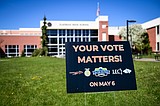
Kalispell Public Schools avoids cuts with passage of high school levy
Deer Park bond rejected
Voters in the Kalispell Public Schools high school district approved a $2.97 million general fund levy request on Tuesday, snapping an 18-year streak of rejecting such requests.
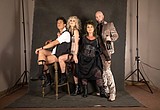
Tune in to the next cheeky episode of Whitefish Cabaret
With a satiric song in their heart and a bawdy joke on their minds, the Whitefish Cabaret has slipped into something more comfortable for the summer season.
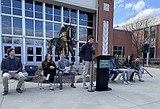
School election ballots due by May 6
Voters are reminded to turn in ballots for school elections.