Working on a better world with composites
Kaye Thornbrugh Nibj Writer | Hagadone News Network | UPDATED 6 years, 9 months AGO
The future of manufacturing is right here in Coeur d’Alene.
That’s what Tyler Alvarado believes. Alvarado is the CEO of Continuous Composites, a Coeur d’Alene-based 3D printing company.
“We’re ready to start telling the story of our technology,” he said.
The traditional 3D printing process turns an object into a design made up of thousands of 2D slices. As the design prints, the slices are stacked together, one at a time, from bottom to top.
Continuous Composites has developed a different method: patented Continuous Fiber 3D Printing Technology (CF3D). A robotic arm moves the toolhead through 3D space, using rapid-curing resins to print unsupported, complex structures into free space.
It’s a game changer. Alvarado said CF3D “will change how cars and buildings look,” opening up design possibilities that are impossible to achieve using traditional 3D printing methods.
CF3D can also embed functionality with fiber optic sensors and copper wire for powering electronics. These 3D-printed structures can sense and react to environmental stimuli, such as heat or pressure, in real time.
“It’s like printing the nervous system,” Alvarado said. “You can use that data to optimize the performance of the composite structure.”
Alvarado pointed to bridges as an example of what might be transformed by CF3D. Bridges look the way they do largely because they must: They’re engineered to hold their own weight.
Now, Alvarado said, imagine printing a composite bridge — extremely strong yet lightweight, not limited by what parts can be created using a mold. How might that bridge look?
Chris Whalen, Director of Marketing and Design at Continuous Composites, used airplanes as an illustration. Attaching the wings to the fuselage adds material, weight, labor and time. But what if the wings and fuselage could be created together, 3D printed as a single piece?
CF3D technology will make it possible to print a more efficient plane that’s lighter and uses less fuel, Whalen said, as part of a fully automated process that generates no waste. (In fact, Alvarado said Continuous Composites will complete a new work cell in Coeur d’Alene in early 2019, big enough to print small airplanes and even cars.)
Continuous Composites has 16 employees and is continuing to grow. Alvarado said most of his employees are locals who never thought they’d be able to find software jobs in Coeur d’Alene. Rather than relocate to cities like Seattle for work, they’ve been able to stay in the area.
“We want to create a place where employees enjoy coming to work,” Alvarado said, adding that he aims to attract and retain local talent. “Our focus is on the people.”
It would’ve been cheaper to build on the prairie, Alvarado noted, but it was important to him to contribute to the economic development of downtown Coeur d’Alene. That’s why they settled in at 215 E. Lakeside Ave. Even as Continuous Composites attracts the attention of “huge companies” in the aerospace and automotive industries, as well as the Department of Defense, all of whom want to use CF3D, Alvarado said his focus will remain on Coeur d’Alene.
“When the company is successful, we want that money to be reinvested in this area,” Alvarado said. “One of our goals is changing the lives of our employees and this community.”
Though composite materials are strong — stronger than steel, in some cases, according to tests conducted by Continuous Composites — they’re not commonly used, largely because of the expense of manually laying fiber over a mold.
Whalen pointed out that CF3D eliminates the need for a mold entirely. He said it will eventually make manufacturing cheaper, stronger and more accessible. The applications of this technology are virtually endless, and only time will tell how it will be used.
“The things that will be made with composites will be earth-shattering,” he said.
INFO: continuouscomposites.com
MORE IMPORTED STORIES
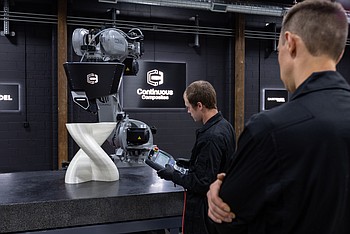
Continuous Composites receives $750K Department of Defense contract
Coeur d'Alene Press | Updated 3 years, 10 months ago
ARTICLES BY KAYE THORNBRUGH NIBJ WRITER
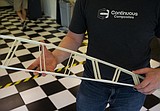
Working on a better world with composites
The future of manufacturing is right here in Coeur d’Alene.
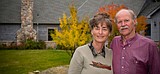
Post Falls bed and breakfast named 'most charming' in Idaho
Everybody has a different story.