Powering affordability
JOEL MARTIN | Hagadone News Network | UPDATED 1 year AGO
Joel Martin has been with the Columbia Basin Herald for more than 25 years in a variety of roles and is the most-tenured employee in the building. Martin is a married father of eight and enjoys spending time with his children and his wife, Christina. He is passionate about the paper’s mission of informing the people of the Columbia Basin because he knows it is important to record the history of the communities the publication serves. | April 25, 2024 7:06 PM
MOSES LAKE — More affordable electric vehicles are on the way.
That was the takeaway from a tour that OneD Battery Sciences offered to a small contingent of Moses Lake community members Thursday afternoon at the company’s SINANODE plant on Road N Northeast.
“Most EVs today are too expensive,” said OneD CEO Vincent Pluvinage. “They cost $40,000, $50,000, $60,000; most people cannot afford it. So we have read in the papers that the growth of EVs is slowing, and the reason is that after the early adopters, you run out of people that have enough money to buy the expensive stuff.”
OneD calls its battery technology SINANODE, a portmanteau word – a word that blends sound and meanings from two words – combining “silicon” with “anode.” A lithium-ion battery consists of a cathode, made of lithium combined with various other metals, and an anode, usually made of graphite. The battery emits electricity by moving lithium ions from the anode to the cathode; the battery is recharged by reversing the process and moving ions back into the anode, according to an article by the U.S. Department of Energy. This means a battery can only store as much power as the anode can hold at one time.
OneD’s solution is to insert silicon nanowires, miniscule strands of silicon about 1/1000 the width of a human hair, into the pores of the graphite to increase the storage capacity. The silicon is obtained by processing silane gas, which is produced at REC Silicon down the road. The storage capacity of silicon is 10 times that of graphite, according to Chief Operating Officer Jan-Marc Luchies, which means that adding 10% silicon to the graphite can double the graphite’s capacity.
This is more efficient than replacing the graphite altogether with silicon, Pluvinage said, because large-scale battery manufacturers are already geared up to work with graphite; OneD’s process enhances an existing product rather than creating a new one.
The research and development work is being done at OneD’s facility in Palo Alto, California, said Luchies. The purpose of the Moses Lake plant is use what the R&D team learns to create a consistent product made to the customer’s specifications.
“We are capable of doing different levels of silicone with a throughput of about 100,000 kilos (about 110 tons) of material,” Luchies said.
The Moses Lake plant is kind of a middle stage, Pluvinage said in an interview Monday. OneD has another facility planned elsewhere in North America that will be able to process 40,000 tons a year, using silane that OneD produces itself.
“All of our customers use different types of graphite, and use different amounts of silicon,” Pluvinage said. “So (we) first start in Palo Alto, where we make smaller quantities, and then they need to qualify that in a large number of EV cell batteries before production, and that will come out of Moses Lake.”
The Moses Lake plant will also serve as a showcase, said Construction Manager Tyson Olson, with a window-lined corridor through the plant that will allow potential customers to observe the process. The plant is essentially set up as a building within a building for safety reasons, Olson said, with an 8,000-square-foot workspace inside of a 12,000-square-foot edifice.
“The reason we have a building-in-building concept is we are dealing with powder, which is graphite,” Pluvinage said. “Every industry with a powder – that can even be sugar – we have to be careful with it; can be even explosive … We also want to make sure that it doesn't get out in the open. That is what’s called containment … On top of that all our equipment and our movement of materials is also always within equipment or confined so we can keep containment.”
The facility was built in an impressive time frame, Olson said, going from a nearly empty building at the end of January to almost ready to fire up this month. Over the next couple of months, Pluvinage said, the company plans to move the rest of the equipment up from Palo Alto and train the Moses Lake crew, and then the plant should be fully operational by the end of the quarter.
“And then it’s off to the races,” he said.
Joel Martin may be reached via email at jmartin@columbiabasinherald.com.
MORE STORIES
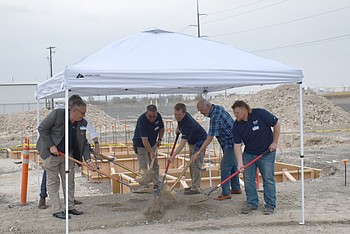
'Holy grail': Enhancement process could make EVs more efficient, practical
basinbusinessjournal | Updated 1 year, 5 months ago
ARTICLES BY JOEL MARTIN
First responders to face off at Guns & Hoses softball game Saturday
QUINCY — The reputations of Quincy’s first responders will be on the line Saturday at the community’s first Guns & Hoses softball game.
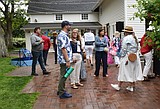
Arts celebration
Nautical-themed CBAA fundraiser weathers a squall and sails on
MOSES LAKE — Mother Nature dealt the Columbia Basin Allied Arts kind of a bum hand Saturday, but the organizers of the fundraiser rode it out with aplomb.
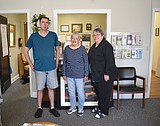
Busy hands: Small core of volunteers keeps Gritman Senior Center serving Ritzville
RITZVILLE — A senior center is sort of like a grocery store or a bank: every town should have one. Big cities have extensive ones, and little towns like Ritzville, well, they plug along through lots of work from volunteers.